
Process Improvement
Process improvement is the systematic enhancement of workflows to boost efficiency, productivity, and overall performance within organizations. It begins with analyzing current processes to identify inefficiencies and bottlenecks, then focuses on optimizing workflows to achieve higher quality outcomes and reduce costs. By streamlining tasks, automating processes, and fostering innovation, organizations can drive productivity gains, improve customer satisfaction, and maintain competitiveness in a dynamic market. Through data analysis, performance metrics, and continuous refinement, process improvement ensures organizations stay agile, responsive, and adaptable to evolving business needs.
Who can attend this course?
- Managers and Supervisors:
- Managers, supervisors, and team leaders responsible for overseeing processes and driving continuous improvement initiatives within their departments or teams.
- Process Improvement Specialists:
- Professionals with a focus on process improvement, including Lean practitioners, Six Sigma Black Belts, and process engineers seeking to enhance their skills and knowledge.
- Quality Assurance Professionals:
- Quality managers, auditors, and professionals involved in ensuring compliance and maintaining quality standards across processes and operations.
- Operations Managers and Analysts:
- Operations managers, analysts, and consultants interested in optimizing workflows, reducing waste, and improving overall operational performance.
- Project Managers:
- Project managers and project team members who want to incorporate process improvement methodologies into their project management practices to deliver better results.
- Anyone Interested in Process Improvement:
- Individuals from various backgrounds who are passionate about improving processes, enhancing efficiency, and driving organizational success through continuous improvement.
Introduction to Process Improvement (9:00 AM – 9:30 AM)
- Welcome and Course Objectives
- Importance of Process Improvement: Enhancing Efficiency, Reducing Waste, and Driving Organizational Success
- Overview of Key Concepts in Process Improvement: Continuous Improvement, Lean Principles, Six Sigma, and Agile Methodologies
Session 1: Understanding Processes (9:30 AM – 10:30 AM)
- What is a Process? Definition, Components, and Characteristics
- Process Mapping Techniques: Value Stream Mapping, Process Flowcharts, and Swimlane Diagrams
- Identifying Process Metrics and Key Performance Indicators (KPIs) for Measurement and Evaluation
Break (10:30 AM – 10:45 AM)
Session 2: Lean Principles and Tools (10:45 AM – 12:00 PM)
- Introduction to Lean Thinking: Principles of Waste Reduction, Value Stream Analysis, and Just-in-Time Production
- Lean Tools and Techniques: 5S, Kaizen Events, Poka-Yoke, Kanban, and Gemba Walks
- Applying Lean Concepts to Identify and Eliminate Non-Value-Added Activities in Processes
Lunch Break (12:00 PM – 1:00 PM)
Session 3: Six Sigma Methodology (1:00 PM – 2:30 PM)
- Overview of Six Sigma: DMAIC (Define, Measure, Analyze, Improve, Control) Methodology and Tools
- Statistical Process Control (SPC): Using Control Charts to Monitor Process Performance and Variability
- Root Cause Analysis Techniques: Fishbone Diagrams, Pareto Analysis, and 5 Whys
Break (2:30 PM – 2:45 PM)
Session 4: Agile Process Improvement (2:45 PM – 3:45 PM)
- Introduction to Agile Principles: Iterative Development, Customer Collaboration, and Responding to Change
- Agile Methodologies: Scrum, Kanban, and Lean Startup Approach to Process Improvement
- Applying Agile Practices to Flexibly and Iteratively Improve Processes Based on Stakeholder Feedback
Session 5: Implementing Process Improvements (3:45 PM – 4:45 PM)
- Change Management Strategies: Overcoming Resistance, Engaging Stakeholders, and Communicating Process Changes Effectively
- Developing Action Plans for Process Improvement Initiatives: Setting Goals, Assigning Responsibilities, and Establishing Timelines
- Monitoring and Sustaining Process Improvements: Establishing Controls, Measuring Results, and Continuously Adapting to Evolving Needs
Conclusion and Q&A (4:45 PM – 5:00 PM)
- Recap of Key Concepts Covered
- Open Floor for Questions and Discussion
- Course Feedback and Closing Remarks
By the end of this course, participants will have gained practical knowledge and skills to identify opportunities for process improvement, apply relevant methodologies and tools, and lead successful process improvement initiatives within their organizations.
[Form id=”6″]
Royal Impact Certification Clients




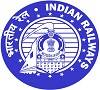




CONTACT US
Get in Touch With Us!
Our Services
- Lead Auditor QMS
- Lead Auditor EMS
- Lead Auditor OHSMS
- Internal Auditor QMS
- Internal Auditor EMS
- Internal Auditor OHSMS
- Awareness Auditor QMS
- Awareness Auditor EMS
- Awareness Auditor OHSMS
Contact Info
Royal Impact Certification Ltd. 623 Tower B, iThum
plot no. A 40
Sec 62, Noida 201301
training@ricliso.com
Call us now:
9355650992
9355650993
Copyright © 2023 RICLTrainingAcademyAll rights reserved.